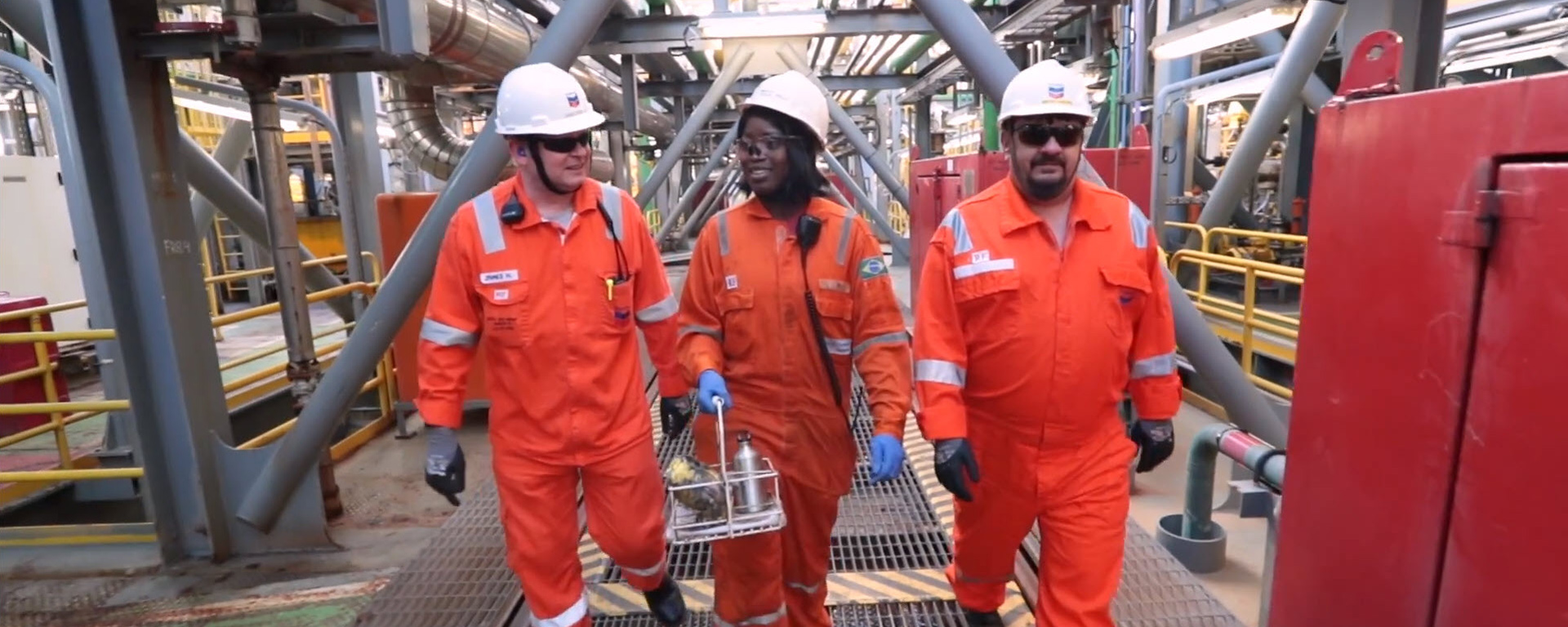
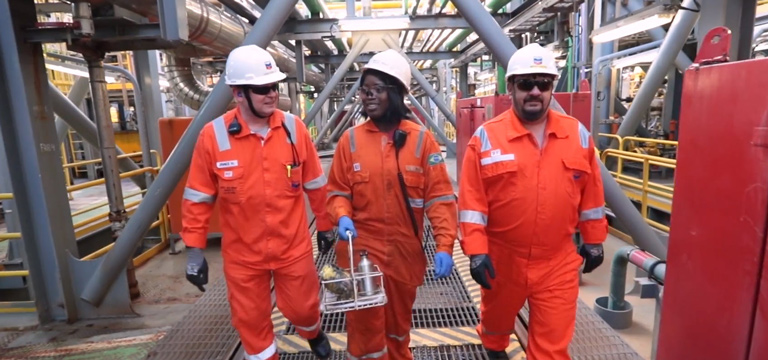
social
diversity and inclusion
Chevron is committed to fostering diversity and inclusion at all levels of our company. It is a cornerstone of our corporate values of high performance, integrity, trust, partnership, and protecting people and the environment. We know that hiring and retaining individuals with an array of talents, ideas and experiences propels the innovation that drives our success. A diverse workforce and inclusive culture help us strengthen areas that need improvement and inspire creative solutions. We believe the attention given to diversity and inclusion makes us more agile, trustworthy and innovative.
Chevron’s diversity and inclusion programs aim to foster a truly inclusive workplace that encourages more meaningful engagement among all employees to strengthen our performance.
recognition
Our diversity and inclusion initiatives have earned recognition from several leading diversity organizations and publications.
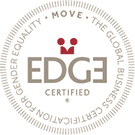
EDGE certification opens in new window
Chevron achieved the EDGE Move Certification level, placing it among the top 14% of 200 global companies receiving EDGE certification for gender equality.
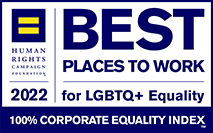
corporate equality index opens in new window
For the 17th consecutive year, Chevron achieved a rating of 100 percent on the Human Rights Campaign Equality Index, which ranks U.S. companies committed to lesbian, gay, bisexual and transgender equality in the workforce.
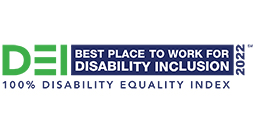
disability equality index opens in new window
The American Association of People with Disabilities and Disability:IN have recognized Chevron with a 100% rating on the 2022 Disability Equality Index, maintaining our top score for the fourth year in a row.
In 2015, Chevron was honored to receive the prestigious Catalyst Award, the premier honor for companies committed to expanding opportunities for women. For more information about the award, visit chevron.com/2015-catalyst-award.
In 2016, Chevron’s Women’s Network launched the Men Advocating Real Change (MARC) initiative developed by Catalyst, a nonprofit that provides resources to engage men as more active and visible champions for gender inclusion. Participants in MARC are committed to achieving workplace gender equality by improving opportunities for women to compete for roles at all levels. Research by Catalyst shows that when men are actively involved in gender diversity, 96 percent of companies report progress. When they are not, 30 percent show progress. MARC programming helps both men and women break down unconscious bias and other barriers to inclusion. In its fourth year, MARC exceeds 3,500 participants – 60 percent of which are men – in 11 countries around the world.
In 2019, Chevron announced a $5 million grant to Catalyst in support of expanding the organization’s MARC program. The Chevron grant will directly support the global expansion of MARC leaders, Catalyst’s immersive training program. It will also support the rollout of MARC teams to Catalyst Supporter companies across the globe, creating a grassroots collective approach that helps men apply their influence to affect positive change in the workplace with respect to gender equality. For more information about Chevron’s grant to support MARC, visit chevron.com/chevron-marc-grant.
we’re working to advance racial equity
In 2020, Chevron made a $15 million pledge to support the Black community in the United States to address barriers to equity. We continue to address racial barriers through education, job creation, talent and leadership development, and community and small business partnerships.
Since establishing our formal racial equity plan, we have progressed the following initiatives:
the women of the human energy company
From rig workers and environmental specialists to engineers and executives, our employees help safely deliver energy to a growing world each day.
what we’re doing
Diversity and inclusion are cornerstones of The Chevron Way values and are critical to ongoing business success. An inclusive work environment that values the diversity of our employees’ talents, experiences and ideas, leads to more innovation and ultimately higher performance. The Chevron Way’s focus on people has helped establish a culture that attracts, develops and retains more diverse talent.
attracting diverse talent
Partnering is critical to our success in attracting talent – we partner with governments, communities and educational organizations across the entire educational pathway. We build trusting and mutually beneficial relationships with strategic partners and are most successful when our partners succeed with us.
We have forged strategic relationships with numerous colleges and universities around the world – developing programs that will empower students and help us to enable human progress.
- Our relationships and programs with historically Black colleges and universities are designed to encourage minority participation in science, technology, engineering and mathematics (STEM).
- We have worked with our university partners to help them improve their diversity and inclusion efforts. We help develop programs to address diversity and inclusion issues and to improve opportunities for women and underrepresented minorities, the retention of students, and the inclusivity environment at their universities. We also partner with the American Society of Engineering Education (ASEE) to convene groups to leverage our efforts.
- We have helped develop a number of programs focused on improving diversity with 4-year institutions and community colleges – STEM Pathway Programs:
- We have awarded numerous diversity and pathways scholarships through universities
- We also partner with diversity associations such as the National Society of Black Engineers (NSBE), the American Indian Science and Engineering Society (AISES), the Society of Hispanic Professional Engineers (SHPE), Great Minds in STEM, Society of Women Engineers (SWE), INROADS, and the National Action Council for Minorities in Engineering (NACME) to develop programs that will help provide internship and full-time opportunities for students.
- Chevron’s Diversity Scholarship Program disburses scholarships to ethnic minorities and women annually through seven partner organizations.
- We support the NSBE’s Summer Engineering Experience for Kids (SEEK) camps in Houston, Texas; New Orleans, Louisiana; and Oakland and Los Angeles, California. The mission of SEEK is "To increase elementary school students' aptitude in math and science and their interest in pursuing STEM (science, technology, engineering, math) career fields, by having them engage in interactive, team-based engineering projects."
To help improve opportunities in STEM education for young girls, we convened sessions with the National Science Foundation, NBC Learn, and more than 15 professional and diversity associations to develop the Women in Engineering Educational Outreach and Training curriculum to arm teachers with materials on engineering that will help expand the pipeline of talent.
We have an incredibly talented workforce willing to share its knowledge in our various mentorship programs. All employees have the option to find a mentor on their own or with the help of a supervisor, through programs specific to their business unit. Our employee networks also offer formal mentoring programs.
In 2019, almost 20,000 employees – nearly 45 percent of our regular workforce – participated in Chevron’s employee networks that celebrate and promote diversity. These networks act as a resource for attracting and retaining talent and enhance Chevron’s reputation through community activities and outreach. They also provide formal mentoring programs and offer opportunities for skill building and career development.
To help ensure that our employees understand our policies and know how inclusion is practiced throughout our company, we provide opportunities such as diversity training, guidance on personal diversity action plans and lunchtime diversity learning sessions.
supplier diversity program
In 2019, we spent more than $650 million on goods and services from woman- and minority-owned businesses in the United States. We spent more than $1.8 billion on goods and services from U.S.-based small businesses.
employee network groups: open to all employees
Our employee networks bring essential value to the business. In 2018, more than 19,000 employees — more than 40 percent of our regular workforce — participated in our employee networks:
- Asian Employee Network
- Black Employee Network
- Boola Moort Employee Network (Indigenous Australian focused)
- ENABLED Employee Network (ENhancing ABilities and LEveraging Disabilities)
- Filipino Employee Network
- Native American Employee Network
- PRIDE Employee Network (Promoting Respect, Inclusion & Dignity for Everyone)
- Somos Employee Network (Latin America and Hispanic)
- Stages Employee Network (Mid and Late career)
- Veterans Employee Network
- Women’s Employee Network
- XYZ Employee Network (Early and Mid career)
Our Chairman’s Inclusion Council provides employee network presidents with a direct line of communication to the Chairman and Chief Executive Officer, the Chief Human Resources Officer, the Chief Diversity and Inclusion Officer, and the enterprise leadership team. The council allows executives and network presidents to collaborate and discuss how employee networks can reinforce Chevron’s values of diversity and inclusion.
our greatest asset is our people
We invest in our workforce and culture, with the objective of engaging employees to develop their full potential to deliver energy solutions and enable human progress. We promote a culture of feedback within the workforce and develop leaders to sustain and strengthen our culture for the future.
We regularly conduct employee surveys to assess the health of the company culture. Recent surveys indicate high employee engagement. Our survey frequency enables us to better understand employee sentiment through-out the year and gain insights into employee well-being. For the latest figures, view the 2022 Supplement to the Annual Report.
leadership in the making
Our development programs are designed to help people achieve their full potential, accelerate leadership capabilities and cultivate a diverse and robust talent pipeline in an ever-changing work environment.
Because Chevron believes in developing leaders at all levels, we aim to grow workforce leadership through a variety of programs, including:
Offering live, one-on-one coaching sessions and Coaching Circles™ with small groups of peers. Since its launch in 2020, Chevron has provided coaching to more than 2,900 supervisors, managers and individual contributors in 45 countries and 18 languages.
Addresses headwinds faced by multicultural women in their leadership journeys. The program promotes acceleration of women’s leadership development and experience.
Promotes acceleration of women’s leadership development and experience.
Address topics unique to demographic groups and enhance leadership and other skill sets essential to success. In 2022, nearly 135 employees participated in Asian American, Asia Pacific, Black, and Latino programs.
For the latest figures, view the 2023 Supplement to the Annual Report.
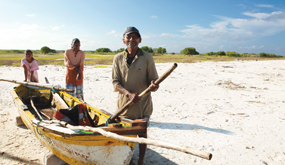